Before you can decide which jib crane will work best for your facility and application, it’s important to take a few specifications into consideration. To start, what do you need the jib crane to do? Once you have established its general purpose, you can decide how it should be mounted. If you are looking for multiple jibs to cover various workstations throughout your facility, for example, your dealer will most likely recommend wall-mounted systems. However, if you are looking to supplement a larger overhead crane or to free up use of other material handling systems in your facility, your dealer may recommend a bridge-mounted or mast-mounted jib crane. Deciding on your installation needs also involves looking at your facility. If your factory floor is particularly small or cluttered, using a wall, column, or bridge-mounted system is a great solution to free up ground space and avoid introducing more obstacles.
There are hundreds of jib crane types available, depending on the crane manufacturer. But for the purpose of this blog, we will look at three common overhead jib cranes, which all differ to meet the needs of your operation. In addition, each jib type has its own set of sub-characteristics, and each can be modified for a specific purpose. This makes customizing the perfect system for your application easy and efficient.
Jib Crane Types
If we’re looking at overhead cranes for the purpose of covering particular workstations, supplementing a larger overhead crane, or merely to generate a circular coverage area in one small section of your facility, there are three basic jib types that are commonly used: wall-mounted jibs, floor-mounted jibs, and articulating jibs. All three jib types can be broken down into specific installation categories and customized to meet your needs.
Floor-Mounted Jib Cranes
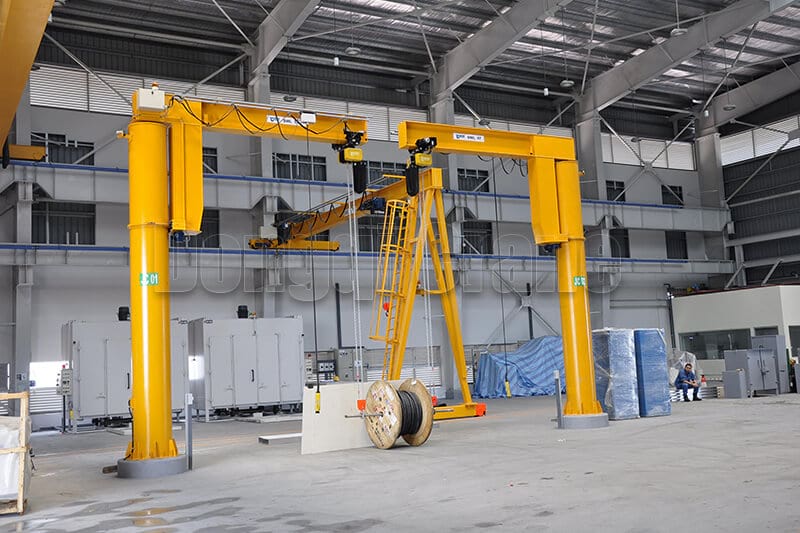
There are many types of jib cranes under the category of floor-mounted and each serves its own unique purpose. For instance, a freestanding (also known as a stand-alone) jib crane is foundation-mounted, which means that it can be installed almost anywhere – inside or outside. Freestanding systems offer higher capacities, longer spans, and 360-degree rotation to cover a large circular area within your facility. These systems are tough and heavy-duty compared to other floor-mounted types, but they are also more expensive and require a special foundation for proper mounting.
Mast-style jib cranes are also floor-mounted, which means they too provide 360-degree rotation and can be installed mostly anywhere indoors. The main difference between a mast-style jib and a freestanding jib is that the mast-style is bolted to the floor and the existing overhead support structure. This helps to eliminate the cost of a special foundation, which is required for the freestanding system. Mast-style jibs are lower cost and can be fully cantilevered or drop-cantilevered, depending on your facilities overhead structure. A full-cantilever mast-style jib crane provides maximum clearance underneath the crane, because the boom is mounted at the top of the mast. The drop-cantilever mast-style jib crane is almost identical to the full-cantilever system, only it has side-plate connections that allow you to lower (drop-mount) the boom at a specified height on the mast. This is extremely useful for facilities that require additional clearance overhead due to obstructions located below the top of the mast.
Floor-mounted jib cranes are an excellent option—whether they are freestanding or mast-mounted—depending on the needs of your application. However, when floor space is a concern, or if you are looking to simply provide additional coverage for individual workstations, wall-mounted jib cranes are a great solution.
Wall-Mounted Jib Cranes
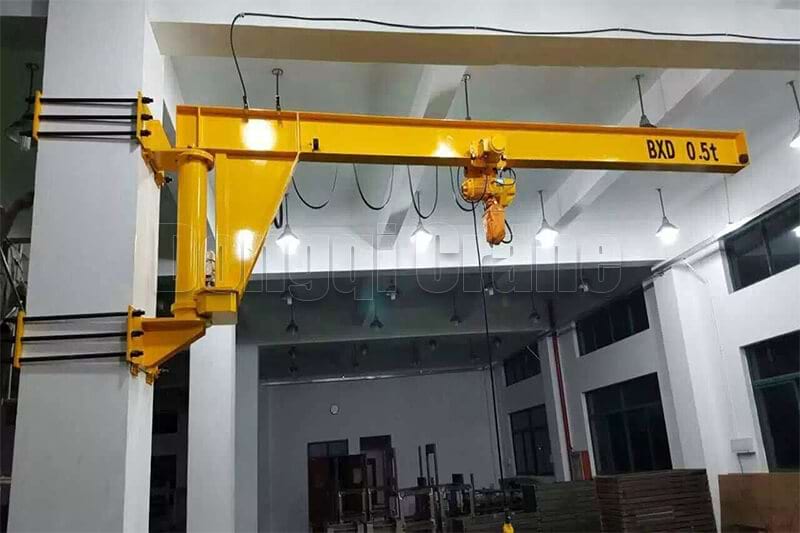
Wall-mounted jib cranes provide 200-degree rotation for a circular coverage area. With capacities up to 5 tons, these systems are not light-weight. However, they’re not nearly as heavy-duty as a freestanding system. Wall-mounted jibs require no floor space and no foundation. They quickly fold out of the way of large overhead cranes and other obstacles, making them a perfect solution for crowded facilities with multiple lift systems.
There are two main types of wall-mounted jib cranes: cantilever and tie rod supported. The cantilever wall-mounted design offers the greatest amount of clearance – above and below the boom. It also transmits less direct force to building columns, making it easy to install on practically any wall or column in your building. The tie rod supported wall-mounted jib crane is extremely economical. It includes no support structure under the boom, so the trolley hoist can easily travel the full length of the boom. This system is reinforced using a wall bracket, along with the tie rod supported boom. The design includes a standard I-beam and single tie rod to eliminate off-center loading problems.
Wall-mounted jib cranes are an excellent material handling solution for busy factories, as they completely maximize space utilization and provide easy installation for individual workstations. But, if you are looking for a system that provides exceptional lift flexibility and precision, articulating jib cranes may be the perfect solution.
Articulating Jib Cranes
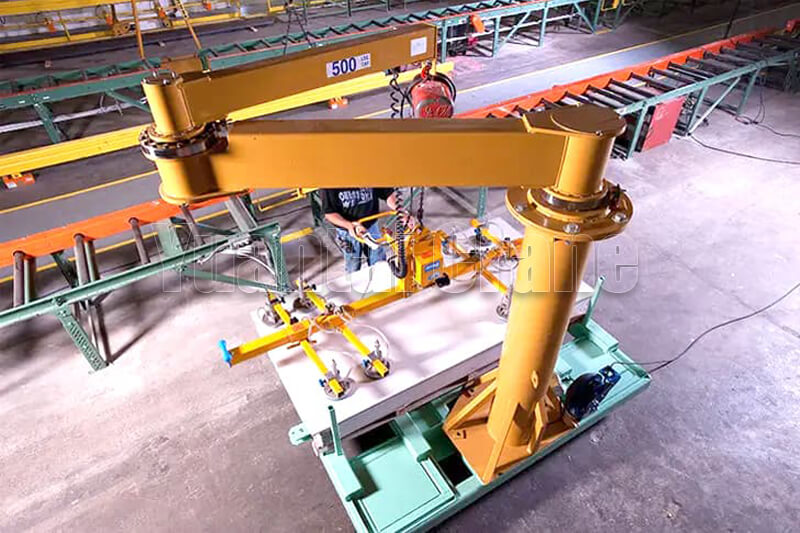
These versatile material handling solutions are able to lift and move loads around corners and columns, reach into machinery, and service virtually any point between the pivot anchor and the far reach of the boom. They offer multiple installation options, including floor-mounting, wall-mounting, ceiling-mounting, and even bridge-mounting. They can support nearly any type of manipulator, balancer, or hoist, and their unique design provides two separate arms for maximum coverage. Articulating jib cranes are designed with an inner arm and an outer arm, allowing them to literally articulate around various parts of a facility, in and out of machinery, and over/under practically any other obstruction. The inner arm provides 200-degrees of rotation, while the outer arm provides 360-degrees of rotation. With multiple installation types and excellent lift flexibility and range of motion, these systems are a great option for nearly any type of application.
No Responses